FAST Continuous
Improvement Program: DMAIC Methodology
FAST is a process improvement training program designed for intermediate level practitioners. It follows the popular DMAIC Methodology, made popular by the Six Sigma Philosophy and with it, we introduce the Yellow Belt Certification. FAST develops your employees and accelerate the rate of improvement.
FAST stands for Focused & Accelerated Solution Tactic
F
A
S
T
F
Focused – It requires a very specific and clear goal and scope, where the problem is well understood and there are general ideas on how to approach.
A
Accelerated – Improvement it must be completed within 2 months of project assignment.
S
Solution – While some data collection and root cause confirmation may be needed, most of the time is spent in finding and implementing solutions.
T
Tactic – Improvement actions are carefully planned to ensure they achieve a specific site goal/objective.
FAST Program Objectives
- Capacitation is focused more on the improvement process than the tools; put the improvement mindset in a framework that helps them move forward in a logical way
- Teams understand project management basic techniques to successfully manage the Lean Sigma project
- Work with teams, rather than individuals; goals are easier to reach when shared; ideas become better with the bounce-back effect of a motivated team
- Teams move fast through the root cause analysis process so they can spend more time on drafting and implementing solutions
Why F.A.S.T.?
Over 90% of the problems can be solved with basic to intermediate problem solving and Lean Kaizen techniques.
DMAIC and Project Management…
a natural fit.
DMAIC is effective in analyzing and improving processes. However, its application commonly face challenges are closely related to project management knowledge areas: lack of management support, insufficient resources and failure to understand the voice of customer (VOC) and scope management. As an option, we also include basic project management to help in the management of the program.
Example of FAST DMAIC & Project Management Training Schedule
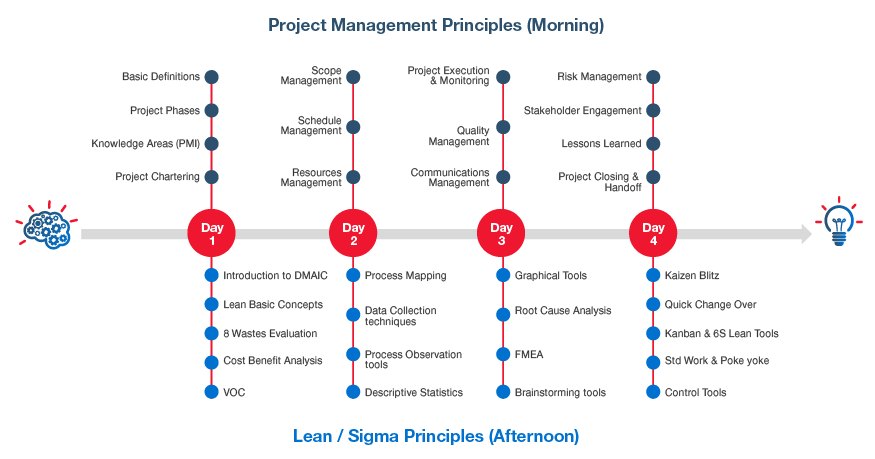
Project Mgmt Principles (Morning)
Lean/Sigma Principles (Afternoon)
Day#1
- Basic Definitions
- Project Phases
- Knowledge Areas (PMI)
- Project Chartering
- Introduction to DMAIC
- Lean Basic Concepts
- 8 Wastes Evaluation
- Cost Benefit Analysis
- VOC
Day#2
- Scope Management
- Schedule Management
- Resources Management
- Process Mapping
- Data Collection techniques
- Process Observation tools
- Descriptive Statistics
Day#3
- Project Execution & Monitoring
- Quality Management
- Communications Management
- Graphical Tools
- Root Cause Analysis
- FMEA
- Brainstorming tools
Day#4
- Risk Management
- Stakeholder Engagement
- Lessons Learned
- Project Closing & Handoff
- Kaizen Blitz
- Quick Change Over
- Kanban & 6S Lean Tools
- Std Work & Poka yoke
- Control Tools
Example of FAST DMAIC & Project Management Training Schedule
Day#1
Project Mgmt Principles (Morning)
- Basic Definitions
- Project Phases
- Knowledge Areas (PMI)
- Project Chartering
Lean/Sigma Principles (Afternoon)
- Introduction to DMAIC
- Lean Basic Concepts
- 8 Wastes Evaluation
- Cost Benefit Analysis
- VOC
Day#2
Project Mgmt Principles (Morning)
- Scope Management
- Schedule Management
- Resources Management
Lean/Sigma Principles (Afternoon)
- Process Mapping
- Data Collection techniques
- Process Observation tools
- Descriptive Statistics
Day#3
Project Mgmt Principles (Morning)
- Project Execution & Monitoring
- Quality Management
- Communications Management
Lean/Sigma Principles (Afternoon)
- Graphical Tools
- Root Cause Analysis
- FMEA
- Brainstorming tools
Day#4
Project Mgmt Principles (Morning)
- Risk Management
- Stakeholder Engagement
- Lessons Learned
- Project Closing & Handoff
Lean/Sigma Principles (Afternoon)
- Kaizen Blitz
- Quick Change Over
- Kanban & 6S Lean Tools
- Std Work & Poka yoke
- Control Tools
We are here to serve
Naturally as a consulting and contracting business, we are where our customers need us, when they need us.